The 3D printing space exists in two parallel universes: the professional one locked behind patents, where printers work magic but cost a few hundred thousand dollars a pop, and the one inhabited by us consumers who must wait decades for ridiculous patents to expire just to print anything but the simplest of plastics.
This doesn’t happen terribly often, but the consumer 3D printing space has a reason to be excited thanks to UK-based 3D printing company E3D’s new Revo hot end. Let’s delve into 3D printing extrusion systems to understand what the fuss is all about.
What’s a Hot End?
It’s easier to understand the concept of 3D printing if you think of it as a baker piping frosting onto a cake. Just like a baker maneuvers a piping bag to print names on birthday cakes, a 3D printer moves the nozzles around to lay down plastic on the build surface.
In fact, the 3D printer extrusion system is quite similar to a baker’s piping bag.
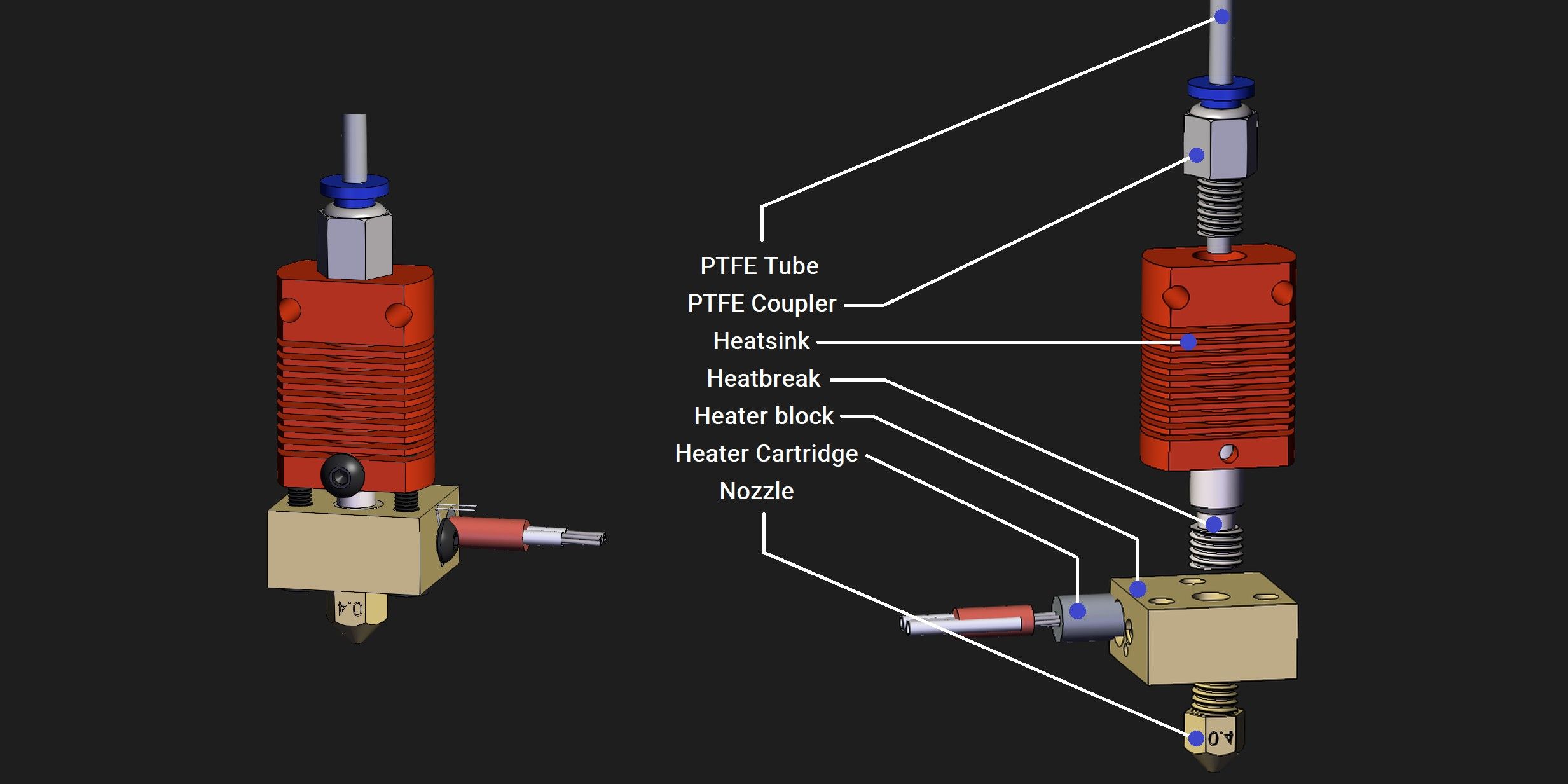
Using your hand to squeeze frosting onto a cake is no different from an extruder pushing filament out through the nozzle. The 3D printer, however, is a bit more complicated. Because plastic doesn’t flow like frosting at room temperature, every 3D printer must be outfitted with a heated nozzle.
This is essentially a high-tech piping bag consisting of an extruder that pushes filament through a heated nozzle assembly, while controlling nozzle temperature and pressure to direct the flow of filament.
The Problem With Existing Hot Ends
Because the consumer 3D printing industry piggybacked on the pioneering work done by the open-source RepRap project, consumer-grade 3D printers take the same DIY-esque approach of using off-the-shelf parts.
The modern hot end design is a great example of this phenomenon.
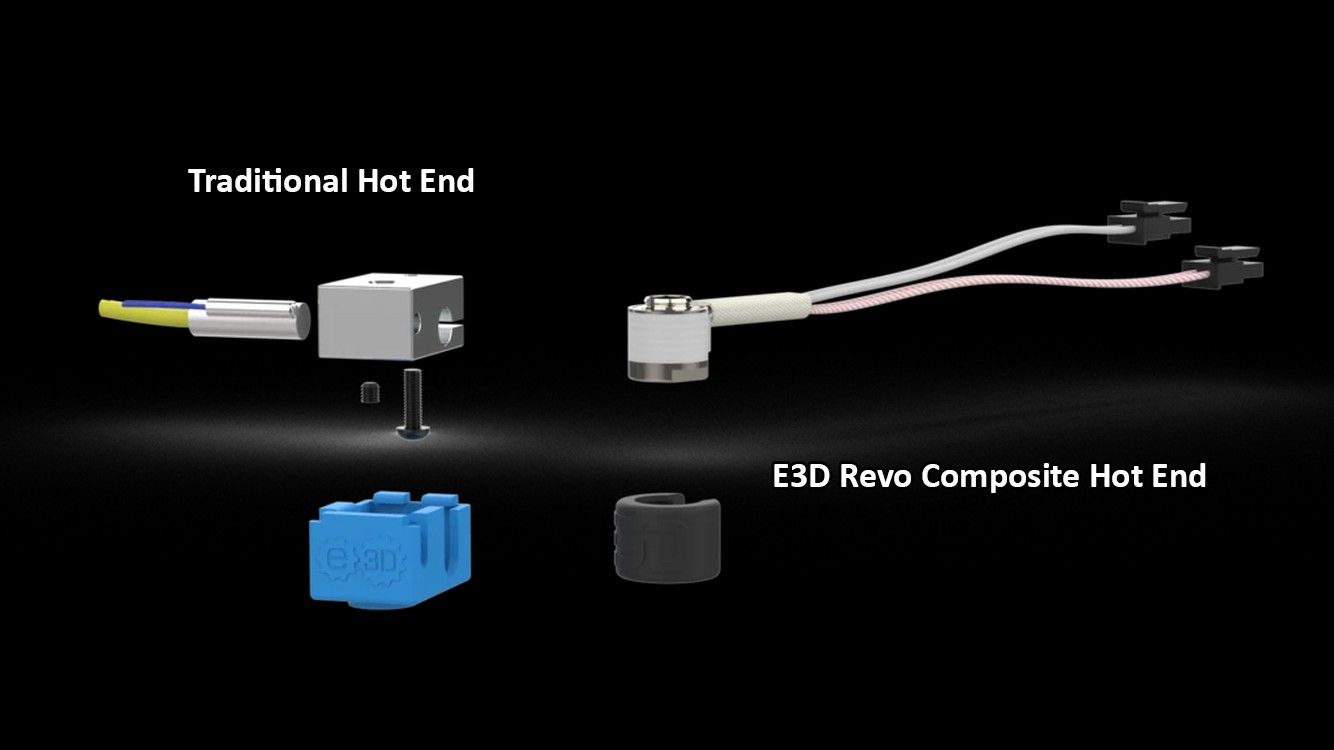
A traditional hot end comprises a nozzle that screws into the heater block, which in turn is heated by a separate cylindrical heater cartridge. The block also houses a removable thermistor for temperature measurement. Finally, a separate heatbreak thermally isolates the hot end from the filament feed path, thereby preventing it from melting en route to the hot end.
Unfortunately, this is a highly inefficient system.
The presence of an air gap between the heater block and thermistor as well as heater cartridges makes efficient heat transfer and accurate temperature control impossible. The increased distance between these elements and the nozzle doesn’t help matters either.
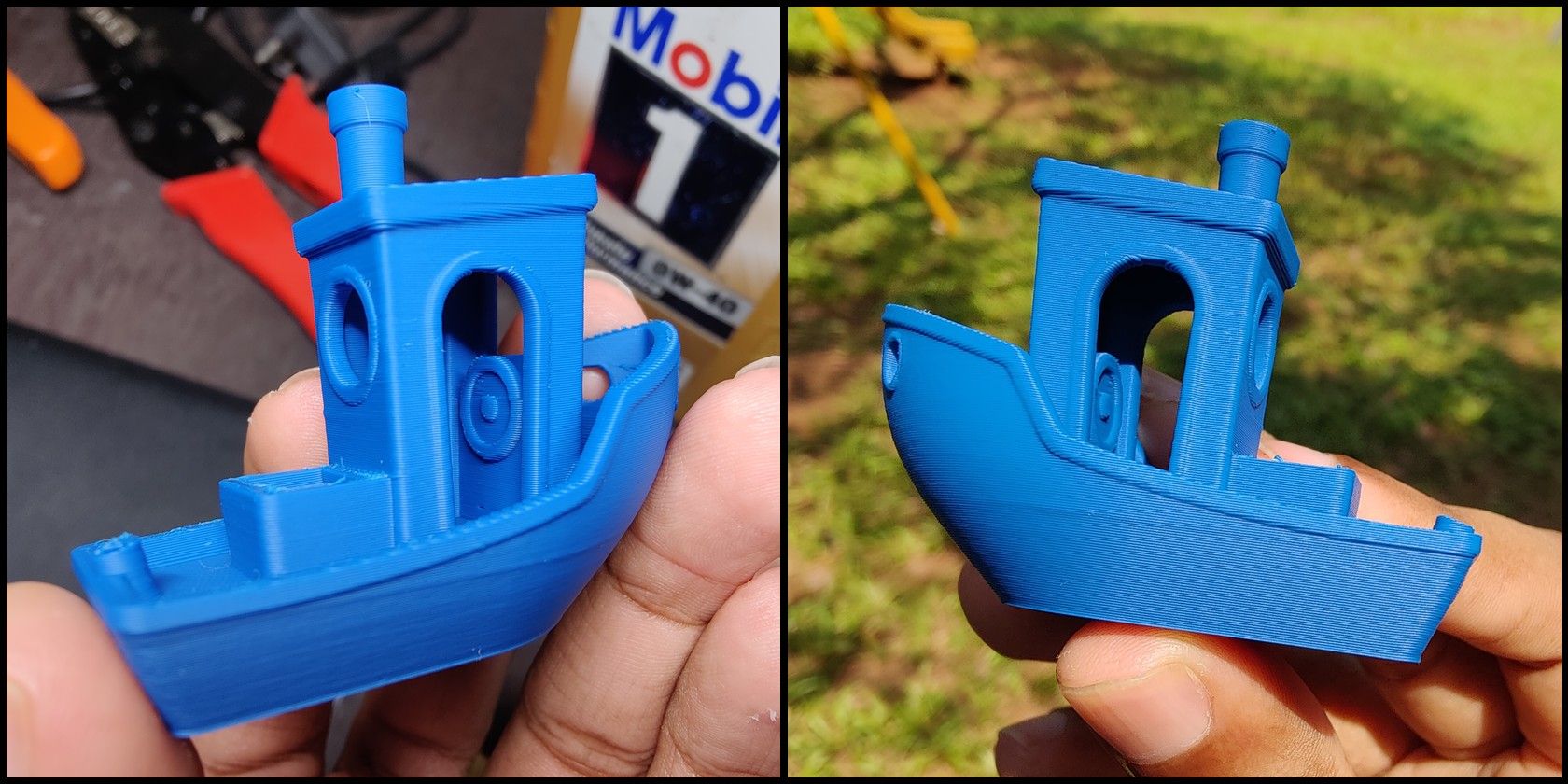
This results in extrusion systems that are incapable of controlling nozzle temperature with any appreciable speed or accuracy.
That’s a major handicap because 3D printing at varying speeds and extrusion volumes isn’t possible without rapid changes in the nozzle temperature required to keep up with the fluctuating filament flow rate.
This, in turn, manifests as a 3D-printing gremlin exhibited by all consumer-grade 3D printers and remains unsolved to this day.
Inspired by Modern Soldering Irons
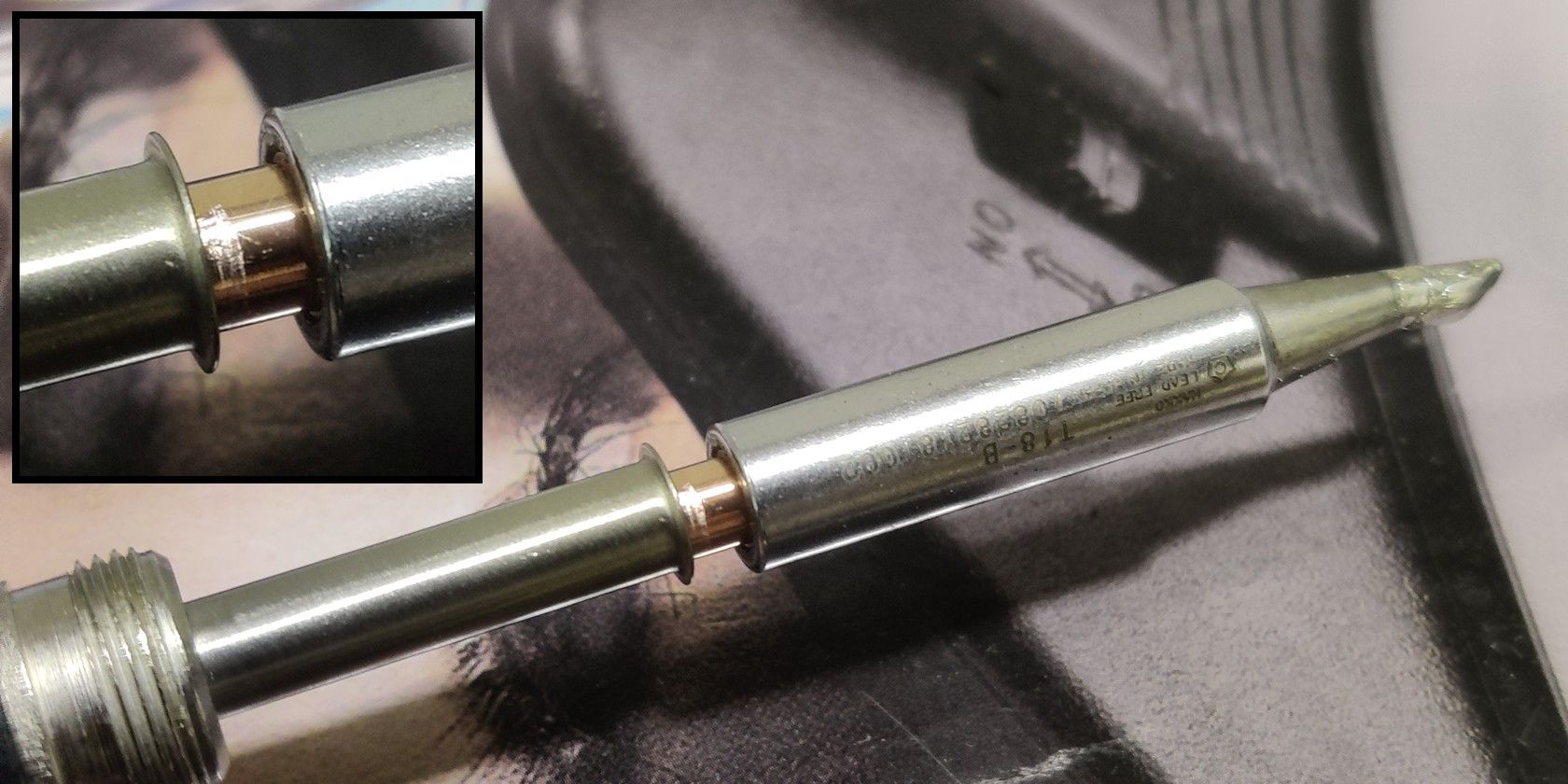
The soldering industry solved this very problem many decades ago by eliminating the air gap between the tip, heating element, and temperature sensor by combining those three elements into a single composite part. Such soldering irons could heat up quicker and solder high-thermal-mass joints with consummate ease.
The Revo hot end takes the same approach by integrating the heater and thermistor into a smaller composite heater core. This solves a number of problems with existing hot ends.
And fixing slow nozzle heat-up is only the beginning, as evidenced by an E3D Revo prototype reaching operating temperatures within a fraction of the time taken by a competing higher-wattage hot end.
The higher thermal efficiency of the Revo heater core has allowed E3D to fashion a significantly smaller hot-end. Its tiny footprint reduces obstruction to airflow from the part cooling fan. This consequently improves the print quality of complicated parts requiring bridging and steep overhangs.
Although some might argue that the lower thermal mass of the Revo hot end’s tiny heater core would make temperature regulation harder, modern soldering irons employing the same approach also opt for designs with reduced thermal mass.
E3D might be onto something here.
A highly efficient heater assembly doesn’t need to store a large amount of heat. In fact, the Revo hot end’s lower thermal mass also allows it to cool down faster.
Rapid, Tool-Less Nozzle Swaps
There’s a good reason why you’d want this hot end to cool down quicker. The reason being E3D Revo's tool-less nozzle swap capability. This is a godsend for a space where the frequency of nozzle clogs is only surpassed by the ensuing disruption they unleash.
Until now, changing a nozzle was a Herculean endeavor involving numerous heat-up and cool-down cycles punctuated by the nozzle requiring hot-tightening at the maximum permissible temperature. Failure to do so would result in more clogs.
Lather, rinse, repeat.
The E3D Revo nozzles, on the other hand, can simply be screwed on and off with your bare fingers. Once the hot end cools down, of course. Because the nozzle and the heatbreak are a single unit, you don’t have to worry about hot-tightening and the associated risk of clogging or plastic leaks.
And this isn’t all about preventing nozzle clogs either.
Varying nozzle sizes also allow you to strike a fine balance between print speed and quality. Want to print a small object with tighter tolerances? Break out the 0.2 mm nozzle. Need to lay down a lot of plastic within a short time? Use the 0.8 mm nozzle instead.
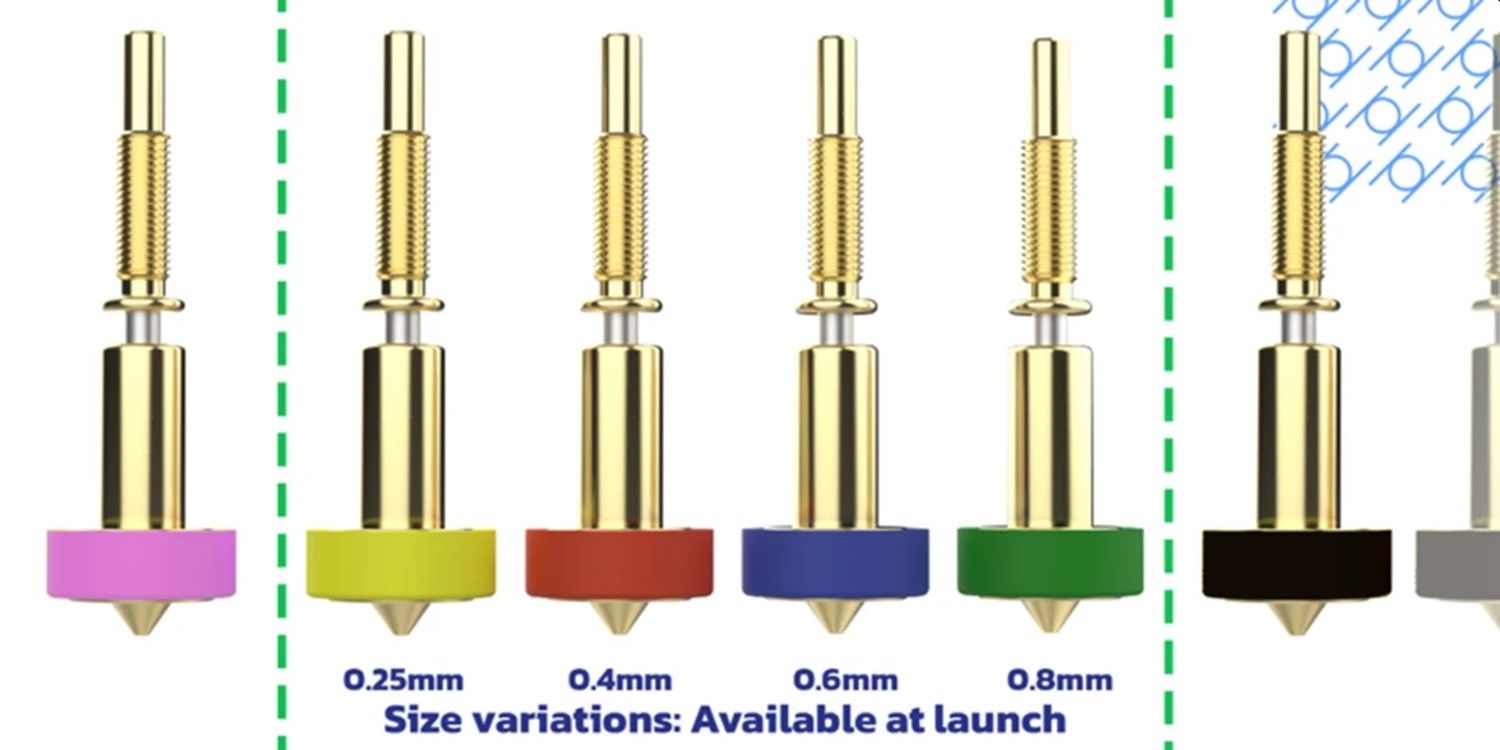
If the Revo ecosystem’s quick-change nozzles really work as advertised, this will finally put tool changes in the 3D printing space nearly on par with those of its high-end subtractive CNC manufacturing counterparts.
Integrated Safety and Rapid Acceleration
Fire hazards are a real concern with 3D printers when temperature regulation faults lead to thermal runway, which subsequently causes the heating element to melt through the heater block and start fires.
The Revo hot end incorporates a positive temperature coefficient (PTC) heating element that ramps up its internal resistance as it gets hotter. This automatically decreases supplied power (heater wattage) as the nozzle heats up progressively. On paper, this should significantly reduce the chances of your 3D printer burning the house down.
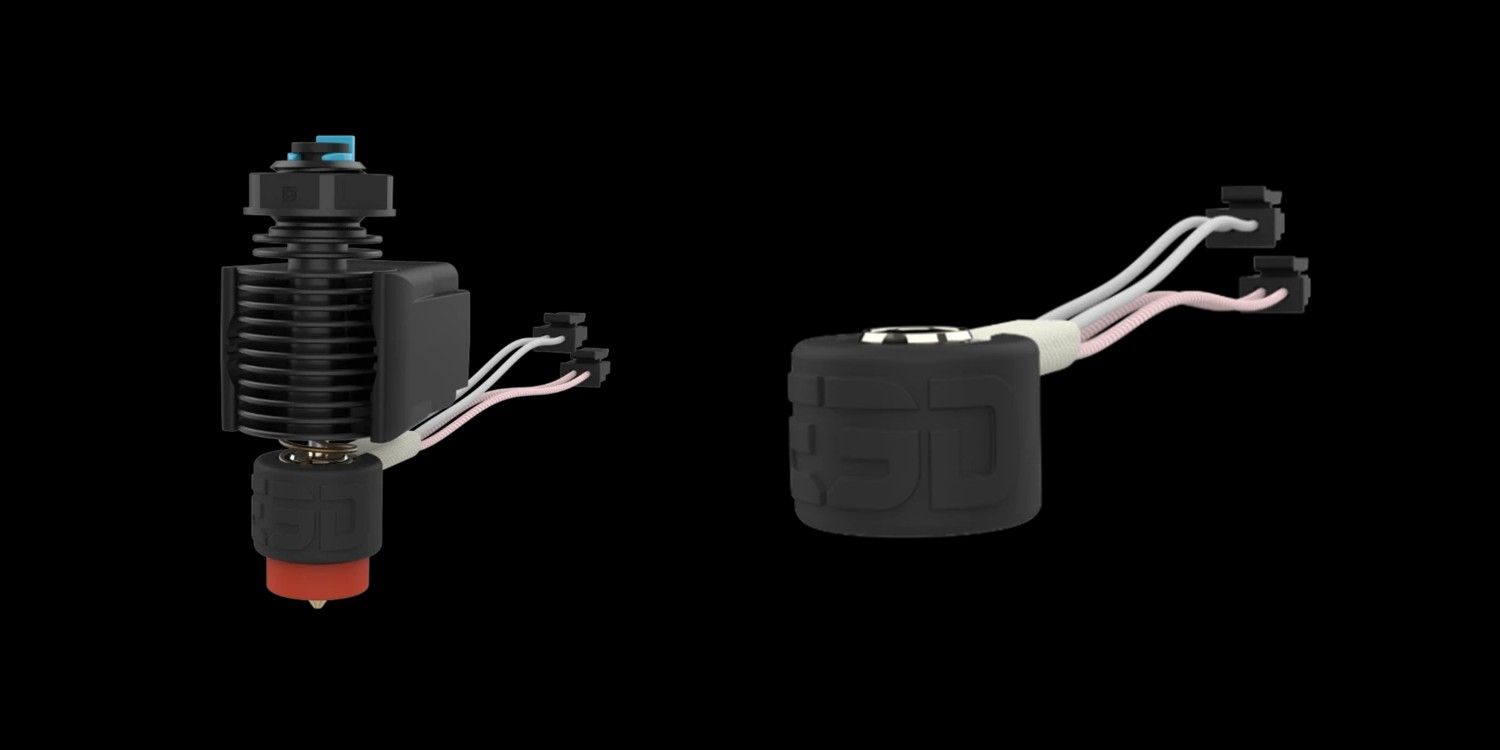
A hot end design with reduced thermal mass has a pleasant side effect of being remarkably lightweight. The Revo hot end weighs in at just 30 grams, which makes it possible to dial up the stepper motor acceleration values without worrying about vibration.
This should allow printers to reach their maximum speeds for a longer duration of the actual print moves, while also reducing ringing and other quality-sapping 3D printing artefacts associated with flinging around heavier hot ends at high speeds.
On the durability front, the heater and thermistor cables are reinforced with a steel-armored strain relief. This should come in handy when contending with massive print failures that necessitate molten plastic to be pried off the hot end. Only this time around you are less likely to inadvertently rip the cables off.
E3D Patents: The Good News…
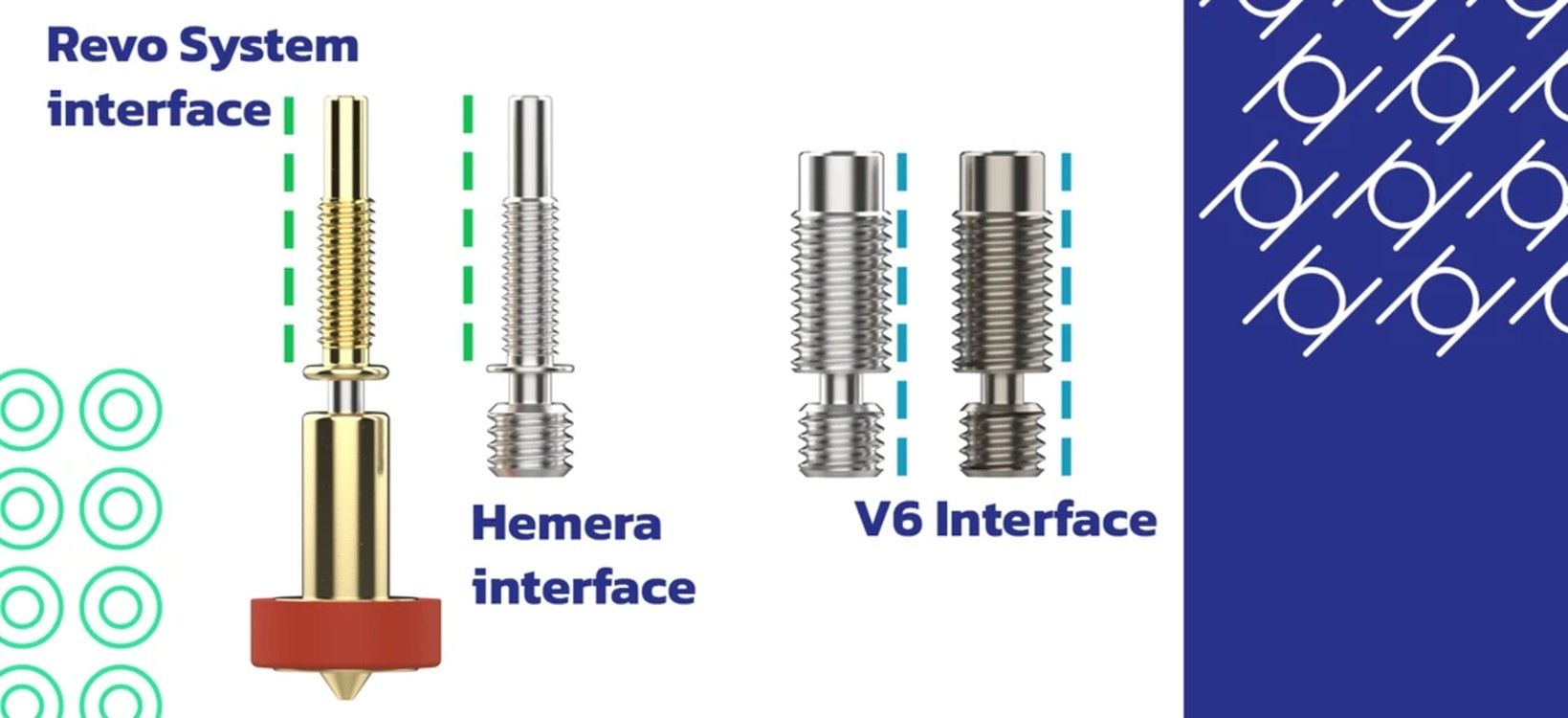
The UK-based company has been committed to the open-source philosophy and has been releasing engineering resources necessary for the 3D printing community to modify and integrate its offerings into other DIY and open-source projects.
While the Revo Micro is the new hot end design, the Revo Six is a drop-in replacement for ubiquitous E3D V6 hot ends found in a large number of consumer and DIY 3D printers. That means practically everyone running E3D hardware has an upgrade path to the new Revo extrusion ecosystem.
This tradition will continue with the Revo, because E3D has chosen to make the cold side interface open source. That should help 3D printing enthusiasts design their own heatsinks and mounts for the Revo nozzles and heater cores.
In other words, open-source 3D printers such as Rat Rig, HevORT, HyperCube, the Voron line-up, and others can be easily updated to integrate these potentially game-changing hot ends in the near future.
…And the Bad News
On the flip side, E3D argues that rampant IP theft has compelled it to file for and (in the future) enforce patents on unspecified aspects of the Revo extrusion system. However, it also promises to desist from litigating against individuals, researchers, academia, and non-profit organizations using its designs to further 3D printing technology.
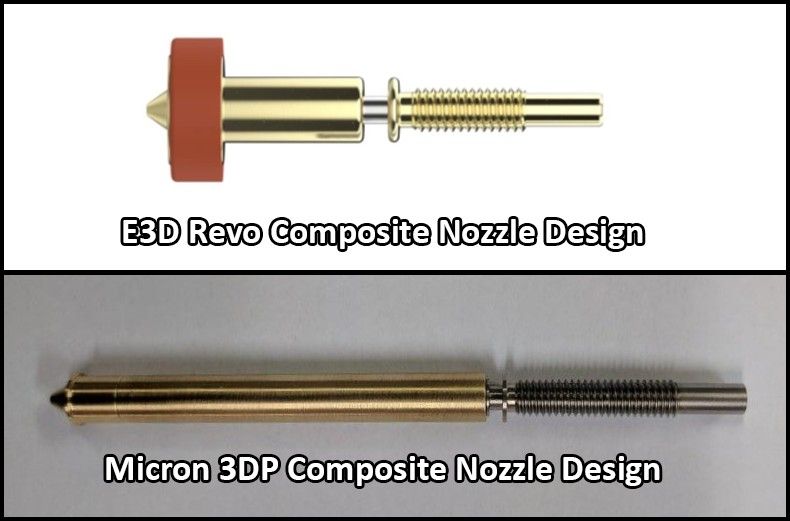
Since E3D’s patents haven’t been published as of this writing, one can only guess whether it will pertain to the unified heater core or the composite screw-in nozzle design bearing an integrated heatbreak.
Unfortunately, both hypothetical patents would be in violation of the company’s promise to avoid filing “the broadest, widest patents that block people from also contributing to technical progress”.
The unified heater core combining the heater and temperature sensor into a single unit has been used in the soldering industry for several decades now. Meanwhile, a 3D-printing patent already exists for a fairly similar screw-in nozzle design sporting an integrated heatbreak.
We have contacted E3D for clarification on the subject and will update this article as and when we hear from them. At any rate, a potentially revolutionary extrusion system replete with four nozzle sizes for $120 definitely deserves the hype leading up to its launch.
0 Comments